‘DF Lean overcoming resistance.’
For the Netherlands Cancer Institute/AVL Decision Free Solutions provided the project leader to realise predefined targets. Only to find out the targets were invented, causing strong resistance within the department before anything had happened. DF Lean overcame the resistance.
Case field
Decision free solutions
Date
November 6, 2016
Location
Amsterdam, The Netherlands
Click for the basic info of this case
- Decision Free Solutions provided project leader for Lean project at the Netherlands Cancer Institute/AVL, Amsterdam
- Project was lead time reduction in providing diagnosis by department of Pathology
- Targets had already been predefined, the department had no description of 'Value', and did not distinguish between the various medical specialisms requesting a diagnosis
- The department's pathologists found the targets grossly unrealistic and saw no need for the project (whatever their performance, specialists would always demand more)
- Decision Free Solutions defined the Value of the department and did a survey among 53 medical specialist to identify their needs
- Decision Free Solutions analysed the data to determine developments in work load over last ten years, and to establish lead times for the various subprocesses
- Workload appeared to have doubled over ten years, different specialisms were identified to have different needs, overall lead-times were much greater than assumed, and for lead time reductions 'revisions' and the subprocesses following the lab-work had to be targetted
Background – Decision Free Solutions was contracted by the Netherlands Cancer Institute/AVL (Amsterdam, the Netherlands) to be the project leader of the ‘Lead time Pathology’ project, one of several projects part of the hospital’s ‘Healthcare Logistics Programme’. The programme requires the project owner to define project goals up front, in part to be able to assess whether the project is aligned with the programme’s ambition of improving several logistical aspects in healthcare, in part to force the project owner to think about the potential for improvement.
The project owner of the ‘Lead time Pathology’ project was the operational manager of the department of pathology. The pathology department itself consists out of various laboratories and a number of specialised pathologists to make a diagnosis (yes/no cancer, type of cancer) based on the analysis of a patient’s tissue (histology) or cells (cytology). The ‘customers’ are predominantly the hospital’s medical specialists. An important element in the process is the dependence, in some cases, on receiving the patient’s sample from the hospital that referred the patient to the Netherlands Cancer Institute/AVL – these type of investigations are called ‘revisions’.
Defined project goals – The project owner defined as the goal a lead time improvement of 20% for ‘regular’ histology procedures and improvements of up to 50% for lead time reductions obtaining samples from other hospitals (revisions). It is assumed that any improvement in the lead time, from requesting to making the diagnosis, will have a positive effect on i) how the quality of the department is perceived by the medical specialists, and ii) patient treatment outcome.
Situation as found in the department – The department had no definition of the services it was providing or supposed to provide (no ‘Value’ defined). The department has an extensive database going back to 2007, registering time-stamps of all process steps from receiving the sample to filing the pathologists report. This database was not used to assess performances. In introducing the project to the people working in the labs there was a general scepticism towards anything ‘Lean’, and when introducing the project to the pathologists there was close to an open revolt to the project. The pathologists felt already pressured by their workload, didn’t see room for improvement over and beyond perhaps 5%, felt that the medical specialists would never be satisfied no matter how much they improved (it would never be quick enough).
Explaining the DF Lean approach – In separate sessions with the project owner and the pathologist it was explained that, as the set goals were not substantiated to be realistic, nor clear to contribute to improving Value to the medical specialists, the definition of the project goals had to be done from scratch. In this process, to take away as much resistance from the department as possible, all decisions were to be avoided, hence all choices in determining both the processes to be improved and the goals to be achieved had to be substantiated. The analogies and differences between the systemic approaches of Lean and Decision Free Solutions, and how the method of DF Lean addressed several weaknesses of Lean, was explained. See Table 1 below.
Implementing the DF Lean approach – Step 1 and 2 of the 10-step method of DF Lean (see Table 2 below) were executed. The activities to be undertaken by Decision Free Solutions were the following:
- Describe the environment and its dynamics surrounding the pathology department (the system)
- Define the overarching Value of the department (to be approved by the project owner and the head of the department) and do interviews with several specialists, followed by a survey among all the medical specialists, to determine their priorities with respect to the various elements of the defined Value
- Analyse the development of the work load of the department from 2007-2015
- Identify the main process to analyse in detail
- Use the database to determine existing lead times of all the involved subprocesses of the identified main process.
Describing the department’s environment – The department’s internal and external environment was analysed and visualised and to visualise the potential impact on the department a ‘Dynamic-Impact diagram’ was developed. Several IT projects were identified which would affect some of the subprocesses in the department, excluding them a priori from optimisation. The ‘competitive edge’ was identified as a factor to be monitored by the department as it directly impacts hiring policy and is closely linked with maintaining the overall aim of ‘excellence’ of the Netherlands Cancer Institute/AVL. Technological developments already were being monitored but were not expected to have an impact on the department for the next several years.
Defining the Value and survey results – Following interviews with several specialists the value was defined and approved, and a survey made. In total 53 medical specialists took the survey and the main results were the following:
- The expected and desired services to be provided by the pathology department dependent strongly on the particular specialism (e.g. gynaecology and thorax oncology departments have different needs)
- Having a reliable estimate of when the diagnosis comes scored higher across the board than ‘as quick as possible’ (8.1 to 7.5), and correlated with department
- The specialists expressed a strong desire to be informed on developments within the pathology department (9,4)
- The reason for reducing lead times was much stronger linked to improving patient experience (9,1) than to improving patient outcome (5,7), again with a strong correlation with department
Analysis of workload development and identification of main process – Whereas the number of requests by specialists had remained largely the same from 2007 tot 2015, the actual number of samples to be made and analysed had increased from 62’000 to 130’000 in this time frame, and the number of medical trials associated with the requests had increased from 120 to 1500. It was also shown that the number of histology analyses was twice as large as the number of cytology analyses, and that the number of histology analyses grew with 7% annually, whereas the number of cytology analysis remained the same.
Identifying the process with largest lead times – From the work load it followed that the histology analyses process was the main process to reduce lead times for. The lead times of the involved processes was statistically analysed (including mean and lead time to process 80% of requests) and is shown in Figure 3. The largest lead times by far concerned the waiting time till a patient’s sample arrived from another hospital (revision), and those processes following the preparation of the samples in the laboratories and thus involved the pathologists.
It was also established that the lead times as defined at the beginning of the project were not corroborated by the data. One analysed lead time took twice as long as the estimated lead time, and a second lead time concerning revisions was so much shorter that the predefined goal would have already been achieved.
Impact of DF Lean’s Definition step on resistance within the department – Following the analysis of the environment, the definition of the Value and the response of the survey, the analysis of workload and of the lead times of the various subprocesses, it was now clear which subprocesses to target in order to reduce lead times. It was also clear that, depending on the department doing a request for a diagnosis, having an accurate prediction of when the diagnosis will be ready is more important than actually reducing the lead time itself.
In coming to these conclusions Decision Free Solutions had taken great care to avoid any decision making, and the data presented left little to no room for interpretation. The impact the data had on the department, especially the pathologists, was such that resistance against the project disappeared.
The pathologists now saw substantiated that their workload had indeed increased considerably more than the number of FTE’s had increased since 2007, something that had not been acknowledged before. The survey results were interesting to the extent that it was shown that overall the hospital’s medical specialists valued a reliable estimate of date of receiving the diagnosis over simply ‘as quickly as possible’, and identified the departments for which shorter lead times were expected to result in better patient treatment. This indicated that a different prioritisation of the work might already improve the department’s Value as defined by the medical specialists.
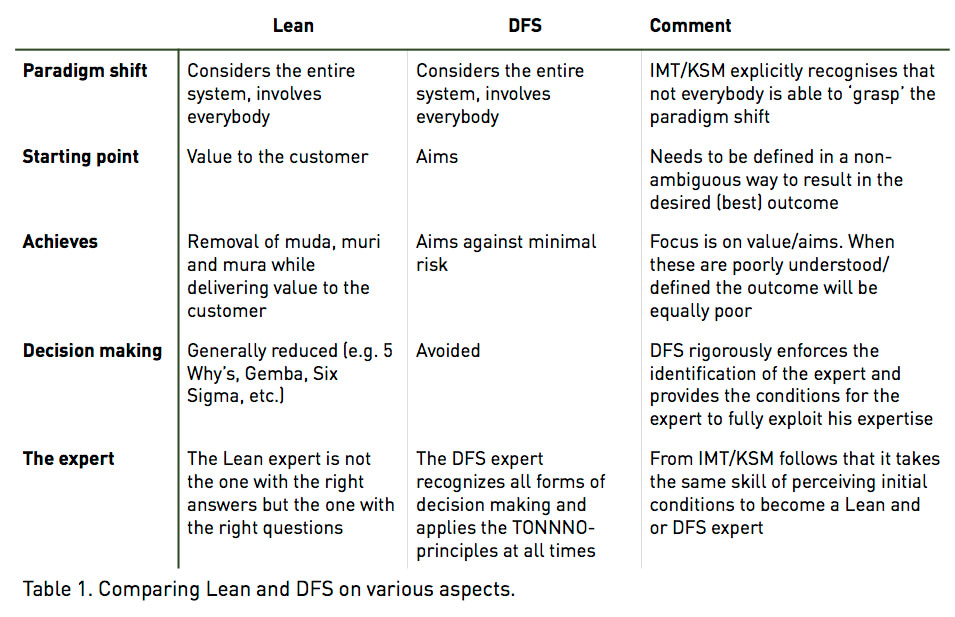
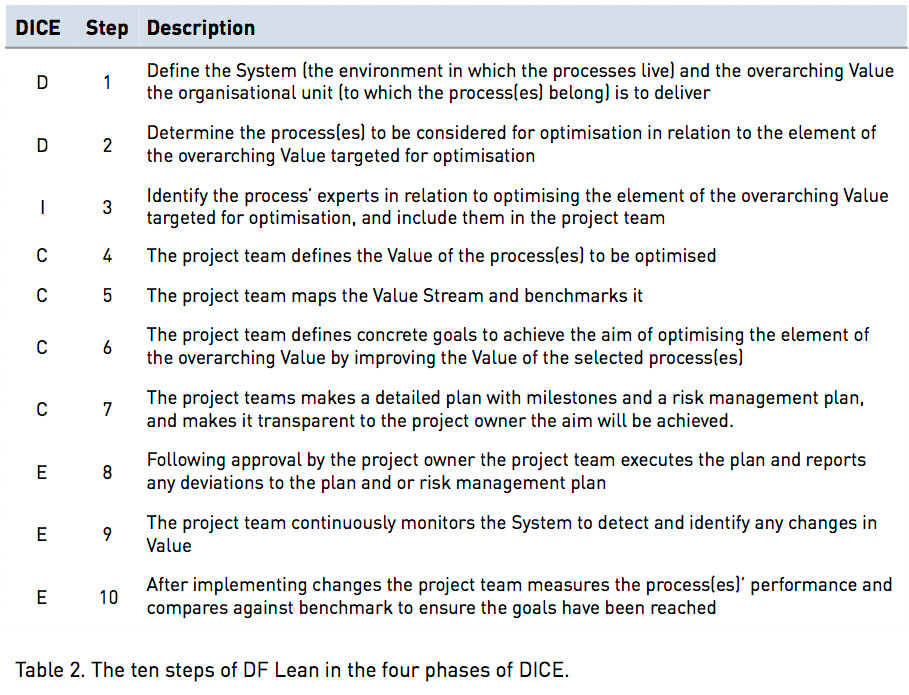
That decisions increase risk is not semantics, it is logic.
That decisions increase risk follows from the dictionary definition and use of logic. Few experience decisions in this way, for various obvious reasons. These reasons don't take anything away from decisions increasing risk. The risk is for real.
Read moreEverybody can manage risk, only few can minimise it.
In every organisation there are both identified and unidentified risks. To manage identified risks is straightforward. Everybody can manage identified risks. Which leaves the unidentified risks. Who will minimise these? Not everybody can.
Read moreDFS helps you to become a High Performance Organisation
Many organisations strive to become a High Performance Organisation (HPO). But what is it, where to begin, where to go? Decision Free Solutions explains what an HPO is (in objective terms), and offers guidelines and practical steps to become one.
Read moreThe alternative to decision making is transparency.
Decisions are conclusions reached after careful thought. When something requires 'thinking' it is not transparent. Transparency allows organisations to manage by approval (instead of decisions).
Read more